FOREWORD
to the reprinting of
“Lead-rubber hysteretic bearings suitable...”
Once upon a time — well, actually, April
1970 — in a New Zealand tea room, Bill met Ivan... and that
was where this particular adventure in seismic isolation
began.
Bill — Dr. Bill Robinson — and Ivan—
Dr. Ivan Skinner — were both members of New Zealand's
Department of Scientific and Industrial Research, and the tea
room in question was part of its Physics and Engineering
Laboratory (PEL) on the Gracefield Campus near Wellington.
Ivan, head of Engineering Seismology, had briefly returned to
New Zealand from a sabbatical in Japan, and told Bill of how
he proposed to use steel dampers in the seismic isolation of
the new design office being planned for New Zealand's
Ministry of Works (MOW), known as the William Clayton
Building.
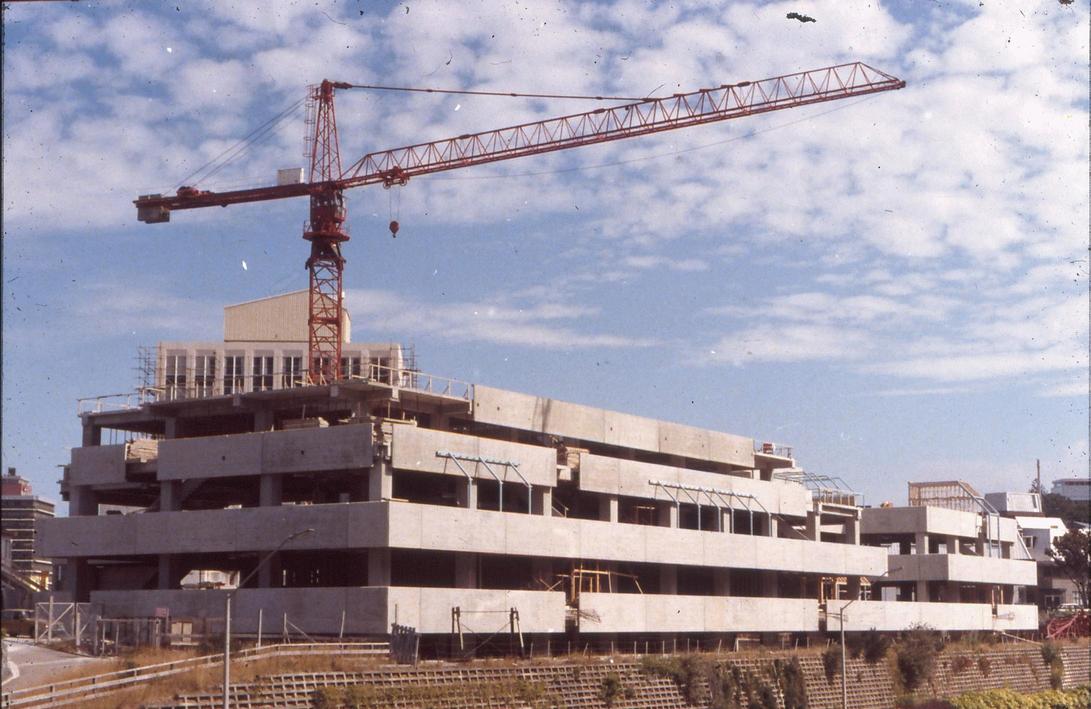
William Clayton Building under construction, 1981.
Bill thought he could find a better
material for damping than steel, so he went back to his
office and spent the next two hours looking carefully for an
element that had a relatively low melting point (∼300°C), was
face-center cubic (fcc), was readily available at a high
purity (impurities ≤100 ppm) — and all at a reasonable
price. The only element that met these demands was lead. Its
relatively low melting point ensured that any plastic
deformation would be healed at room temperature by the
interrelated processes of recovery, recrystallisation and
grain growth, while its fcc meant there would always be a
slip system available to accommodate any deformation and its
high purity would see to it that the plastic deformation
could be maintained and results would be consistent.
The next problem was how to deform lead
so that a relatively large damping force of 1 to 100 tonnes
could be produced. The solution was a lead extrusion damper
(LED). This thinking culminated in twenty-four 25 tonne LEDs
(±400 mm) being manufactured and tested by PEL to
provide the damping for seismically isolating the Wellington
Central Police Station. This 10-storey tower block is
supported on long piles in caissons founded 15m below ground
in weathered greywacke rock. The near surface-soil layer
consisted of marine sediment and fill of dubious quality.
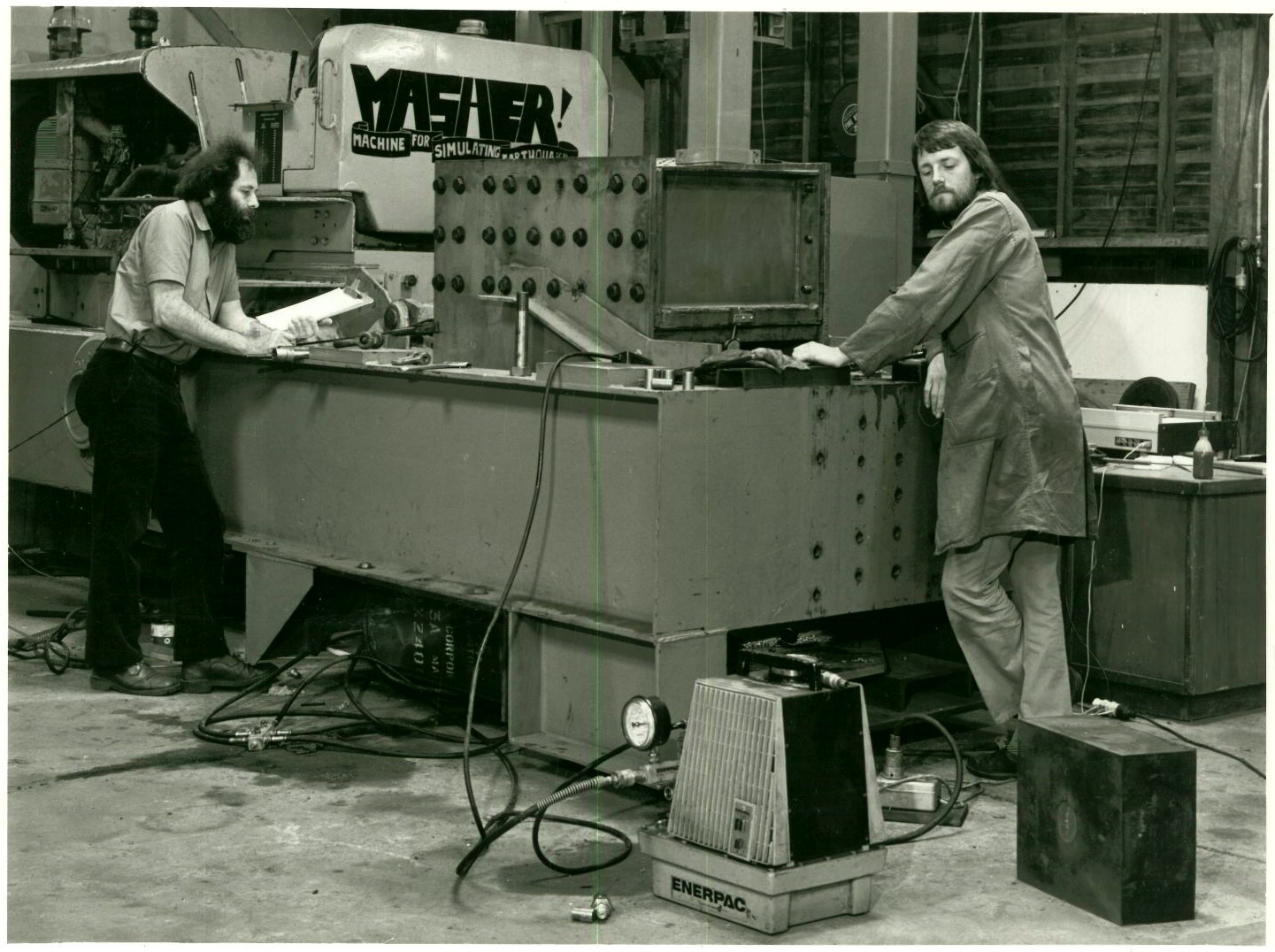
Bill and his technician Alan Tucker operating the MASHER.
The LED, however, was not an elegant
solution for damping the MOW's William Clayton Building, so
instead Bill started trying to make a lead shear damper. But,
no matter what the shape, they always failed after one
quarter of a cycle. Obviously they needed to be supported in
some way. As recorded in Bill's lab book, the solution, which
occurred to him at home on 2 April 1975, was to place a lead
plug through the layers of steel and rubber. It was not until
April 1977, though, that his team was able to obtain two
cemented laminated rubber bearings from the Engineering
Seismology Section, have the workshop drill a 56mm diameter
hole in one, press a lead plug in the hole, and test both in
an Instron testing machine.
The results were so promising that Bill
immediately contacted the MOW engineers working on the design
of the William Clayton building and they decided to sell PEL
an old D8 Caterpillar tractor to use as the basis of a test
machine. PEL sold the tractor's blade for more than the cost
of the tractor itself and the engineering design team, led by
Cam Smart, designed a rig powered by the >100 KW
diesel engine, capable of providing a vertical load of 300
tonnes and a displacement of up to 91 mm. Bill then
tested a series of bearings of progressively increasing
diameter, until at a lead diameter of 170 mm, after two
cycles the gearbox failed! This result was viewed by all as a
success and enabled the project to proceed. Today thousands
of buildings and bridges worldwide use the lead-rubber
bearing.
References
[Kelly et al. 2011] T. E. Kelly, R. I.
Skinner, and W. H. Robinson,
Seismic isolation for designers and structural
engineers, Robinson Seismic Ltd., Petone, New
Zealand, 2011.
[Skinner et al. 2003] R. I. Skinner, W.
H. Robinson, and G. H. McVerry, An introduction to seismic
isolation, Wiley, New York, 2003.
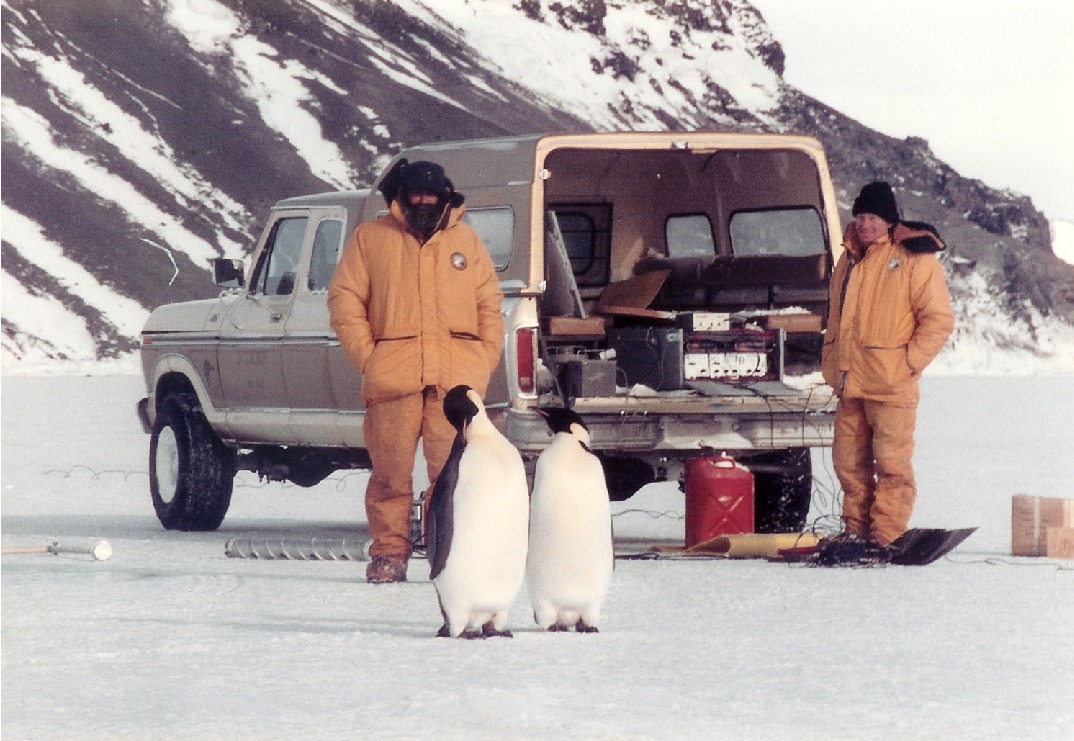
Bill and his colleague, Dr. Michael Staines, on the
sea ice at Tent Island, McMurdo Sound, Antarctica, near
Scott Base. The final version of the paper reprinted on the
next few pages was written while Bill was a research fellow
at Scott Polar Research Institute, Cambridge, England
learning about sea ice.
|